
Envest Product Development
From May to August 2021 I worked as a product developement engineer at Envest Product Developement.
​
Envest is an engineering consulting firm that does product development and supply chain sourcing for various other companies. These ranged from small single person startups, to large multinational corporations.
​
I had a lot of autonomy and responsibility during this coop term. Being a relatively small engineering firm, I had to personally manage several projects with tight deadlines for clients. This lead to some high pressure moments and pretty crazy work hours. All in all it was a great opportunity, and I learned the most here out of all my internships.
​
​
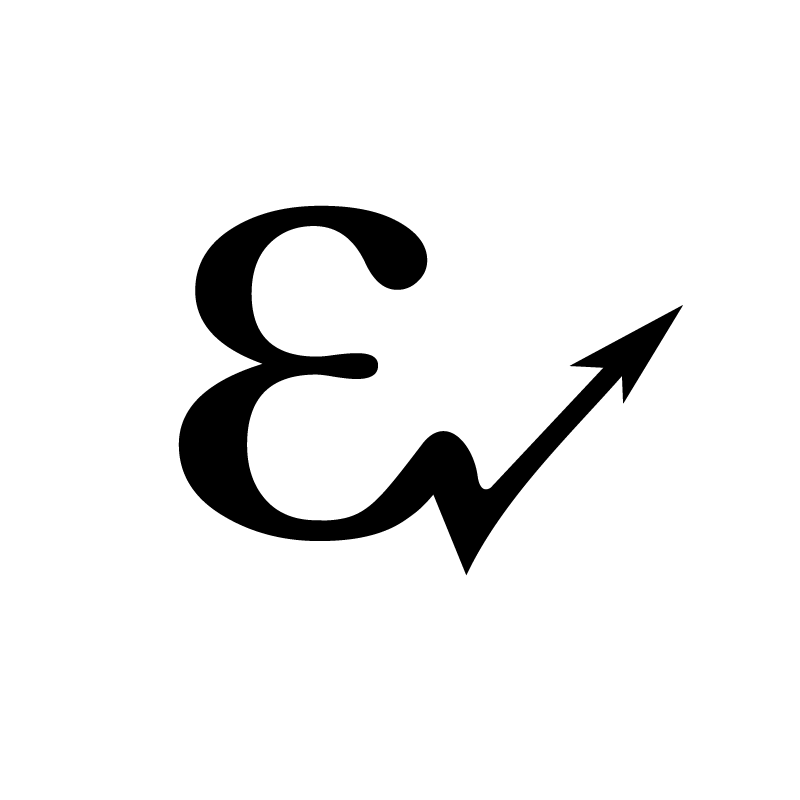
Smart Chair
The biggest project I worked on was the design of a smart chair. The idea of this chair was to automatically adjust to the most ergonomic position of a user, and assist them with their sitting posture. I did a lot of work on this product. I did FEA analysis on critical components to ensure they would not fail. I provided drawings for all the components in the chair. I did supply chain sourcing for mass manufacturing. I designed the drive train, and iteratively physically prototyped it until it functioned as intended. I did tolerance fittings for all the components inside the chair.
​
Overall this was an extremely time consuming and exhausting project. This was my first time working with an industrial level assembly, and I got a lot of exposure to the handwork and difficulties required to make a product functional. Since previously, I had worked a lot with component manufacturers, I am really happy to have worked with a large scale complex assembly.
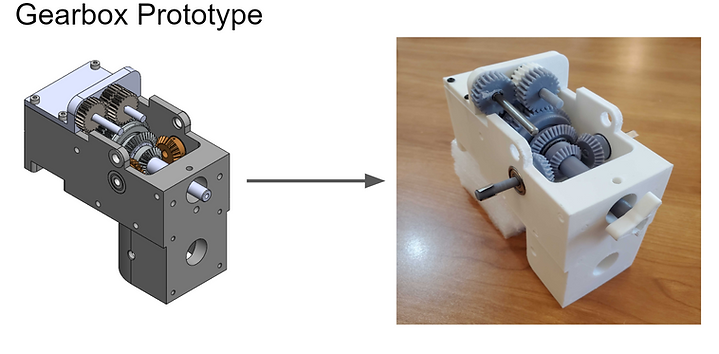


Sensor Housing
I was also in charge of designing sensor housings for various hardware companies such as Mero Technologies. The design went through two phases. The first was designing a prototype and 3D printing it. Once the fit and function was verified we would, ship it to the client company and ensure they were happy with it. Then a mass manufacturable version was designed (injection moldable), and we did the supply chain sourcing.
​
Sometimes I had to make brackets along with the housing. This exposed me to sheet metal fabrication and the various techniques associated with making a good sheet metal part. It also gave me an appreciation for using the various grades of steels and material hardening methods. One of the brackets would become plastically deformed after a few cycles of use, so I had to design around it and come up with better design. This process involved both changing the geometry of the bracket itself along with looking into strain hardening methods for steel.
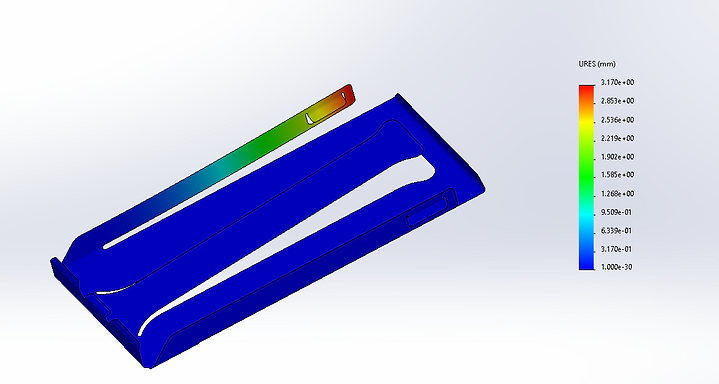

